- Home
- PCB
-
PCBA
- High-density PCBA (with BGA)
- RF PCBA
- Industrial control equipment PCBA
- Inverter energy storage PCBA
- Frequency conversion equipment PCBA
- Medical care PCBA
- Automotive electronics PCBA
- Digital product PCBA
- Internet of things PCBA
- Speaker audio PCBA
- Instrumentation PCBA
- LED lamp driver PCBA
- PCBA SMT patch processing
- PCBA DIP plug-in processing
- Industrial control box assembly and processing
- Application
- Support
- Factory
- News
- About
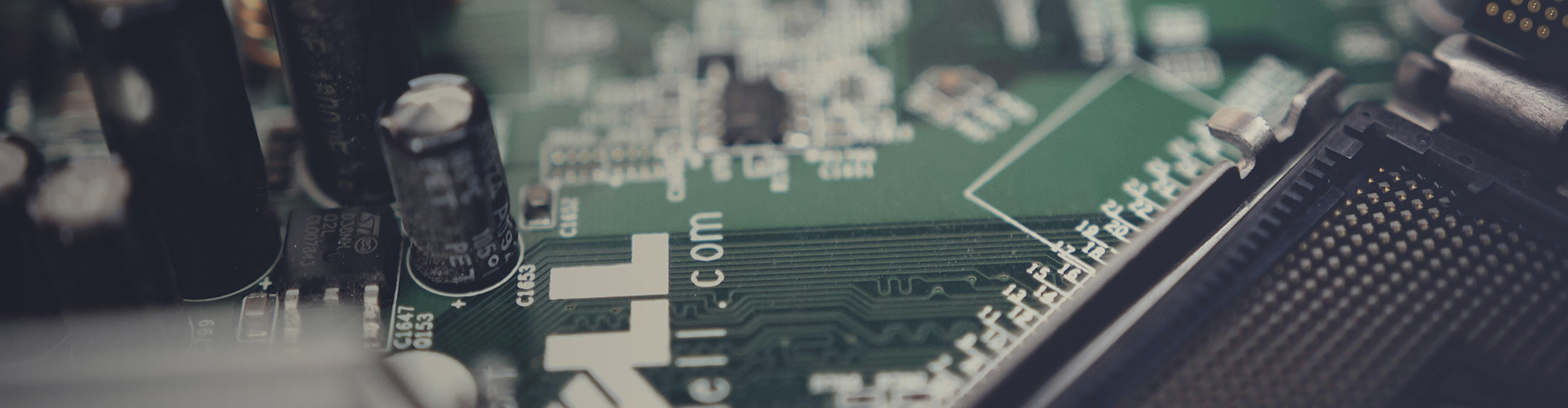
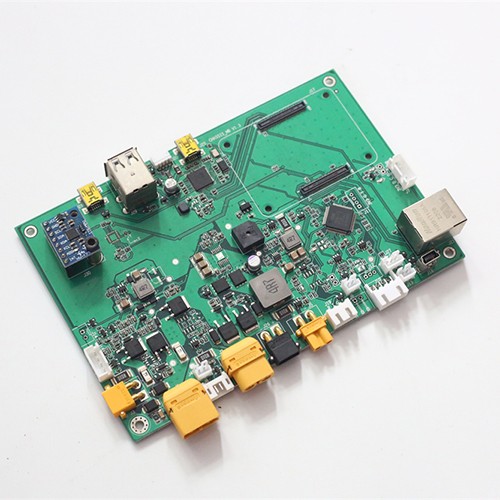
Robot main control system
The PCBA of the robot's main control system needs to be able to withstand vibration, shock, and temperature changes, so environmental factors need to be taken into account during the design.
During the entire assembly process, take appropriate anti-static measures, such as using anti-static wrist straps, anti-static mats, and anti-static packaging.
Use precise soldering techniques, such as selective soldering, wave soldering, or manual soldering to ensure the quality and consistency of solder joints. Visual inspection and X-ray inspection are performed after assembly to ensure that there are no defects in solder joints and components are not misaligned, and to ensure that the PCBA design and manufacturing process meets international safety standards and regulatory requirements
Motion control: Control the movement of each joint and actuator of the robot according to the predetermined motion trajectory and speed requirements. This includes position control, speed control and acceleration control.< /p>
Sensor data processing: Receives information from various sensors , such as position sensors, force sensors, visual sensors, etc., and process and analyze these data. This helps the robot perceive the surrounding environment and make corresponding decisions.
Task Planning: According to Given the mission objectives, formulate the robot's action strategy and path planning. This includes determining the robot's movement sequence, selecting appropriate tools and operation methods, etc.
- Communication management: Communicate with external devices, such as host computers, other robots or sensor networks. This can achieve Functions such as remote monitoring, data transmission and collaborative operation.
Safety protection: Monitoring The robot's operating status ensures that it operates within a safe range. When an abnormal situation occurs, timely measures are taken, such as stopping movement and alarming, to protect the safety of personnel and equipment.
Controller: Usually a high-performance microprocessor or microcontroller, responsible for executing control algorithms and processing various input and output signals.
< /li>Memory: used to store control programs, parameters and data. This can include random Access memory (RAM), read-only memory (ROM) and flash memory, etc.
Input and output interface: connect various sensors, actuators and external devices. This can include digital input and output interface, analog input and output interface, communication interface, etc.
Power Management: The robot main control system provides a stable power supply. This includes functions such as power conversion, battery management and power protection.
Real-time performance: The robot's main control system needs to have high real-time performance and be able to respond to various input signals and execute control commands in a timely manner. This is crucial to ensure the robot's motion accuracy and safety. < ;/span>
Reliability: Due to robot Usually operating in a complex environment, the main control system needs to have high reliability and be able to resist various interferences and failures. This can be achieved by adopting redundant design, fault detection and recovery mechanisms, etc.
Scalability: As robotics technology continues to develop, the main control system needs to have good scalability and be able to easily add new functions and modules. This can be achieved by adopting modular design, open interfaces and software architecture. /span>
Intelligence: Modern robots are the main Control systems are becoming increasingly intelligent, able to autonomously learn and adapt to different tasks and environments. This can be achieved through the use of artificial intelligence techniques, machine learning algorithms, and adaptive control.
< ;/p>
Motion control: Control the movement of each joint and actuator of the robot according to the predetermined motion trajectory and speed requirements. This includes position control, speed control and acceleration control.< /p>
Sensor data processing: Receives information from various sensors , such as position sensors, force sensors, visual sensors, etc., and process and analyze these data. This helps the robot perceive the surrounding environment and make corresponding decisions.
Task Planning: According to Given the mission objectives, formulate the robot's action strategy and path planning. This includes determining the robot's movement sequence, selecting appropriate tools and operation methods, etc.
- Communication management: Communicate with external devices, such as host computers, other robots or sensor networks. This can achieve Functions such as remote monitoring, data transmission and collaborative operation.
Safety protection: Monitoring The robot's operating status ensures that it operates within a safe range. When an abnormal situation occurs, timely measures are taken, such as stopping movement and alarming, to protect the safety of personnel and equipment.
Controller: Usually a high-performance microprocessor or microcontroller, responsible for executing control algorithms and processing various input and output signals.
< /li>Memory: used to store control programs, parameters and data. This can include random Access memory (RAM), read-only memory (ROM) and flash memory, etc.
Input and output interface: connect various sensors, actuators and external devices. This can include digital input and output interface, analog input and output interface, communication interface, etc.
Power Management: The robot main control system provides a stable power supply. This includes functions such as power conversion, battery management and power protection.
Real-time performance: The robot's main control system needs to have high real-time performance and be able to respond to various input signals and execute control commands in a timely manner. This is crucial to ensure the robot's motion accuracy and safety. < ;/span>
Reliability: Due to robot Usually operating in a complex environment, the main control system needs to have high reliability and be able to resist various interferences and failures. This can be achieved by adopting redundant design, fault detection and recovery mechanisms, etc.
Scalability: As robotics technology continues to develop, the main control system needs to have good scalability and be able to easily add new functions and modules. This can be achieved by adopting modular design, open interfaces and software architecture. /span>
Intelligence: Modern robots are the main Control systems are becoming increasingly intelligent, able to autonomously learn and adapt to different tasks and environments. This can be achieved through the use of artificial intelligence techniques, machine learning algorithms, and adaptive control.
< ;/p>
- Previous:Bus network control system motherboard
- Next:Four-port WIFI gateway
+008613530931324
Telephone: +008613530931324
Mail: Gelant.lei@kilandu.com
5th Floor, Building 4, Yibaolai Industrial City, Qiaotou Community, Fuhai Street, Bao'an District, Shenzhen
All rights reserved © 2024 Shenzhen Jintianlei Innovation Technology Co., Ltd.